
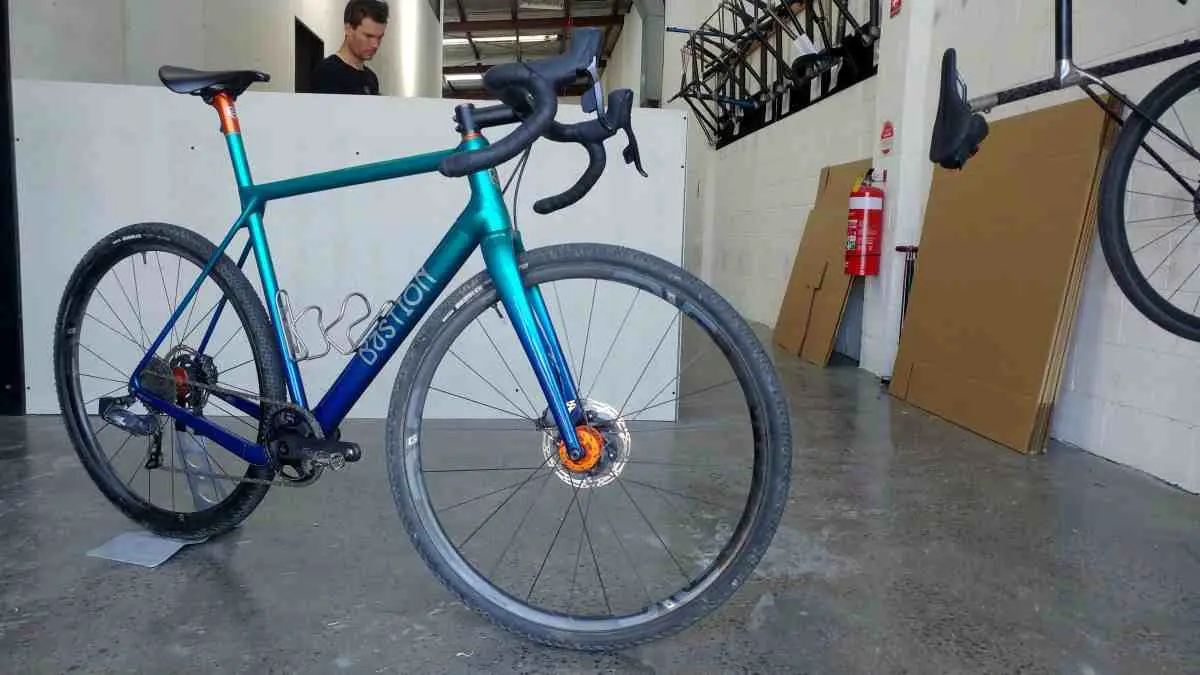
There, they will be put on a physiotherapist’s table to address any injuries or asymmetries they may have before having their physical data measured and recorded.

At Bastion, after an initial chat with Schultz or Woolcock about their requirements, they will spend the next 2-3 hours at Riderfit, one of Bastion’s companion companies at the front of the building. They won’t enter a flashy retail store and view scores of factory-fresh bikes, choosing a few to test-ride and deciding which one they want to take out the door with them. When a cyclist commissions a bicycle from Bastion, they should not expect the experience they might have purchasing a bike from one of the well-known larger manufacturers. This co-operative approach is an intriguing part of their business model, and just one of the ways Bastion likes to do things differently. Schultz says they think of it as an advanced manufacturing bicycle hub because, though there are synergies between the businesses and they send each other work, they share the space because none of them could afford to be there independently otherwise. Bastion empowers the rider to design their own adjustable bike that is a unique fit not only to their desired specifications and aesthetic preferences, but the physical capabilities of their own body with all its ticks and quirks.īastion shares the industrial warehouse it occupies in Fairfield, north-east Melbourne, with three other specialised bicycle-related companies. All keen cyclists, it was a classic case of creating the bike they wanted to buy but which didn’t exist. Bastion Managing Director Ben Schultz recalls how he and his co-founders, James Woolcock and Dean McGeary, wanted to incorporate their three passions: cycling, leading-edge manufacturing and Australian-made production. Last but not least, the 3D printed track crank offers superior aerodynamics and blends seamlessly into the bike frame.Ĭycling Australia will debut the new bikes with 3D printed components at the upcoming Tissot UCI Track Cycling World Cup series, after which they will hopefully be approved for racing at the Olympics next year.After the R&D specialists were handed their notice from Toyota in 2014, they sat down and nutted out a new business concept. The handlebars, customized for length and angle, also improve the bike’s aerodynamics. The Madison bars, for their part, are characterized by a double-drop shape that gives riders the option of several riding positions. For instance, the part is reportedly available in lengths up to 160 mm with varying stack heights and angles.
#BASTION CYCLES PRO#
The 3D printed sprint stems were customized to fit the fork of the Electron Pro bike as well as to the size of rider. The parts also exploit the design freedom afforded by AM through the integration of internal lattices (for lightweighting) and variable wall thicknesses.

In other words, every stem, handlebar and crank part has been tailored to the rider in question, making for a truly customized and optimized bike. The 3D printed components, as reported by Cycling Tips, have each been customized to the cyclist. Together, the Australian’s cycling team and bike manufacturing brand designed 3D printed stems, handlebars and cranksets that would fit the Olympic team’s existing Argon 18 Electron Pro bikes. Since bringing 3D printing technology in house, Bastion has made its AM services available to others in the cycling industry.Ĭycling Australia is one of its recent partners. Paired with strong and lightweight carbon fiber tubing, the titanium lugs enabled Bastion to offer a modular bike frame.įor years, the company worked with external 3D printing services to produce the lugs, although it recently brought metal 3D printing in house with the acquisition of Renishaw’s AM250 3D printer. The company, founded in 2014 by Ben Schultz, James Woolcock and Dean McGeary, pioneered the use of titanium 3D printing for its bikes with the integration of 3D printed titanium lugs. Constructed in partnership with Australian bike brand Bastion, the bikes each feature a set of three 3D printed titanium components: the stems, Madison handlebars and cranksets.īastion is arguably as well known in the cycling world as it is in the additive manufacturing world. When the 2020 Tokyo Olympics roll around, Australia’s cycling team will be mounted on some fairly high-tech bikes.
